
Longread
The road to sustainable plastics by 2050 (part 2)
By 2050 we want to achieve a fully circular economy, with only biobased or recycled plastics. But the law is not sufficiently clear and specific. For example, the government bans one particular type of polystyrene but not another. Simpler and clearer policies are needed, according to Violet Ross, a doctoral student at Environmental Policy and Law in Wageningen.
It is essential that policymakers distinguish between different types of plastic, says Thoden van Velzen researcher of plastic packaging and the reuse thereof at Wageningen Food & Biobased Research. There are dozens of plastics, each with its own properties. These properties should be considered when deciding whether to recycle, burn, or replace with biobased plastics. He explains this using the three most frequently used plastics, PET, PP and PE.
Most commonly used plastics: PET, PP en PE
-
PET (polyethene terephthalate) is a plastic used to manufacture hard bottles
(the well-known PET bottles) and containers. PET’s key characteristic is its
high melting point, which enables recycling businesses to clean the bottles for
reuse. Thoden van Velzen says that recycling of PET should be expanded to
include all PET bottles and containers. However, this means that PET containers
for meat, cheese, fish and vegetarian foods must be redesigned for recycling.
Moreover, it requires the construction of more recycling plants than are
currently available. -
PE (polyethylene) is mainly used to manufacture foils, freezer pouches, bread packaging, and certain vials. It is a soft plastic that melts at low temperatures, complicating recycling and reuse in the food sector. Replacing fossil PE in food packaging with biobased PE could be a first step, according to Thoden van Velzen. Technology to manufacture PE from sugar cane is already available. However, this biobased alternative is considerably more expensive than regular PE. Some food producers, however, opt for biobased material to achieve their climate goals. Financial stimuli and legislation could help phase out fossil PE.
-
PP (polypropylene) is used in butter cups and ice cream containers.
It is a hard plastic with a lower melting point than PET. The biobased
alternative PLA (polylactide) is a polymer made of lactic acid. Dairy business
Friesland Campina aims to replace PP with PLA, but the current recycling system
does not accept PLA. Since the amount of PLA the sorting industry receives is
small, removing it from the plastic waste pile is not viable unless the amount
of PLA increases. Conversely, industries delay switching from PP to PLA until
the recycling system offers recycling options. A recycling lock-in, says Thoden
van Velzen. There are more instances in which the recycling system frustrates
rather than stimulates the development of biobased plastic.
Recycling plastic
Recycling faces a critical issue. Used plastics generally are too varied and polluted for reuse. Consumers fail to adequately rinse the plastics, and producers often use combinations of different plastics which are hard to separate for reuse. The petrochemical industry has a solution: it has invested in pyrolysis businesses that break plastics down into pyrolysis oils, which require only a few additional steps to be reintroduced in
factories in the Netherlands that manufacture new components for existing
plastics PET, PE and PP.
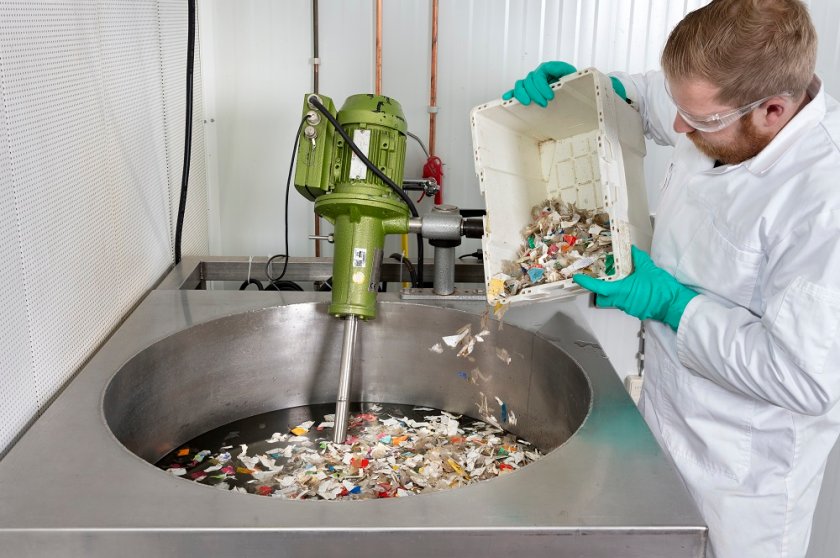
This may appear to be a simple solution for plastics that are hard to separate, says Thoden van Velzen. The method has several drawbacks. ‘In the first place, it does nothing to address consumers discarding plastics, so the planet continues to be polluted. Secondly, the pyrolysis that breaks down plastics into new building blocks is almost as harmful to the environment as incineration and fortifies the interests of the petrochemical industry.’
Recycling is the first alternative to pyrolysis. This, however, requires the collection of plastic waste. Not just PET bottles and containers but also durable plastics used in computer and car components. ‘In those sectors, plastics recycling is common, and may be increased’, Judith Van Leeuwen says, researcher at WUR’s Environmental Policy group. ‘I assume tyres will not be prohibited but recycled. Increasing the durability of products would really help.’
A second alternative is further developing degradable biobased plastics. ‘I believe this is the only viable solution for packaging that is likely to become litter’, Thoden van Velzen states. He expects a circular biobased economy without fossil resources in 2050. That option may also have adverse effects. Are there sufficient plant-based resources for biobased plastics? Van Leeuwen says, ‘Biobased plastics may end up competing with food, since there is a limit to how much land can be used for plant production’. Hence, we must keep as much of these plastics in circulation to dampen the need for new plastics.
Complete reset of the current plastic system
How do we arrive at the desired situation with barely any fossil plastics in 2050? Thoden van Velzen argues that this requires ‘a complete reset of the current system because the current system for producing and recycling plastics is based on fossil resources. We must alter the entire infrastructure and facilitate a new agro-industry to supply the required resources. We are currently in the investigative stage, a period of chaos, and, in this transition process, we face higher costs and losses.’
He calls for three major decisions in this transition.
- First, a ban on the export of plastics. The Netherlands exports considerable volumes of plastics to other countries, thus creating invisible pollution. Former deputy minister Stientje van Veldhoven of Infrastructure and Water Management curbed the export of plastics to countries lacking a processing infrastructure and developed initiatives to address this issue within the European context, he states. The goal is for Europe to tackle its own plastic consumption.
- The second major decision that is needed is to require manufacturers to produce plastic products and packaging that can easily be recycled. At present, plastic packaging is often made up of different types of plastics, labels and adhesives. That ultimately leads to some 200 million different types of packaging made up of various components. ‘It’s a mishmash, the price of the freedom in packaging that no one considers.’
Cleaning machines in the recycling industry are regularly jammed due to the presence of unexpected interferences. And adhesives that prevent the labels from being rinsed off are still used. Additionally, the packaging may contain banned inks, plasticisers or chromium-6. ‘The solution lies in simplifying packaging and using as few as possible plastic combinations.’ - The third essential measure is to force the recycling sector and plastic manufacturers to jointly invest in the recycling of biobased packaging. The waste processing industry has trouble with the small streams of biobased waste because it complicates the separation process. This, however, frustrates the production of new biobased packaging. A biobased alternative to styrofoam, made from paper fibres, is available for use in the protective packaging of electronics. This material could be discarded in the paper bin, but Paper Recycling Netherlands refuses to accept the biobased alternative. ‘Accepting such initiatives will help slowly build a biobased economy.’
Violet Ross,a PhD candidate in Environmental Policy and Law in Wageningen, adds a fourth policy measure that could reduce the use of plastics. Policymakers must increase their focus on durability. Now that single-use plastic cutlery is banned, the manufacturer will produce plastic cutlery that can be washed in the dishwasher and used up to 150 times. Sounds great, but this more durable product is still often discarded after a single use, rendering the legislation ineffective.
Ross says a life cycle analysis could also lead to keeping the plastic cutlery. If wooden cutlery is shown to have a larger ecological footprint and higher CO2 emission than plastic cutlery, this alternative may well be reconsidered.
Ross argues that circular systems are only sustainable if they lead to lower consumption. Which leads us to a fifth factor: how do we re-educate consumers? Communication and increasing awareness are not enough. The effect of communication is overrated, according to Thoden van Velzen. ‘After fifty years of separating biowaste, paper and glass, we must still explain what goes where…’. Van Leeuwen sees opportunities, provided the focus lies on developing new routines. ‘That means businesses and shops should change how they present their products. Albert Heijn, for example, is increasingly presenting fruits and vegetables without plastic packaging, forcing consumers to adjust their routines and how they buy convenience foods. Perhaps we should limit the range for simplicity.’
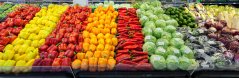
Ross appeals to businesses to change their earning model. ‘Businesses need a new philosophy. Coca-Cola now sells most of its products in PET bottles. This company is investing in taps for businesses and universities, enabling staff members to use biobased cups. This costs a fair sum because PET bottles are cheap and taps are expensive.’
Coca-Cola’s policy is in keeping with the servicisation strategy. Businesses sell a service rather than a product. The energy provider no longer sells batteries but charging stations where batteries can be recharged. IT businesses no longer sell mobile phones but sell memberships that include the use of a phone. The phones remain the property of the business, which is responsible for their durability and reuse. Clothing shops are emerging where clothing can be rented. An interesting and radical business strategy to reduce the use of plastics, says Ross.
Curbing the use of disposables
The government can deploy additional legislation to encourage this business strategy, Ross states. The EU Eco Design Directive, for example, states that consumers have a right to repair their products, meaning that producers must supply spare parts to replace broken parts of computers and household appliances. If the product breaks within 10 or 20 years, the responsibility rests with the manufacturer, hence increasing the product’s lifespan.
The EU is also preparing legislation for a mandatory product passport containing information on the types of plastics contained in the product, how they must be recycled, and whether they are biodegradable. A barcode on all plastic products could increase the lifespan of plastics. But it is really about curbing the use of disposables, say the researchers.