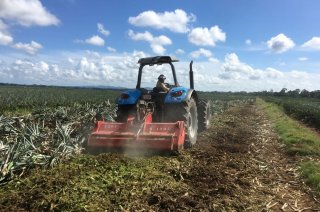
How to make circular use of agricultural residues?
By-products from the agrifood sector are increasingly being put to other uses. A new assessment framework, co-developed by Wageningen University & Research scientist Wolter Elbersen, helps to select the more circular application.
Until two generations ago, there was often a pungent smell in the air in the north of the Netherlands. It was produced by the potato processing industry, as it discharged potato juice into the surface water. The juice, a waste product of the production of potato starch, polluted both the water and the air. But this juice also contains 3% valuable proteins. It was a typical example of an unused agricultural residue, but today the valuable proteins are recovered for use in food products.
Agricultural residues are by-products of agriculture or the food processing industry such as sugar beet leaves and cashew shells. They are often left behind on the fields, but are also burned in the open air. “Agricultural residues are still a cause of nuisance and pollution today,” says Wolter Elbersen, researcher at Wageningen Food & Biobased Research. “Burning straw in the fields in India and Egypt leads to severe air pollution, sometimes even forcing airports to close. Leaching of nitrate and phosphate into ground and surface water is another example. By giving agricultural residues circular applications, these problems can be avoided and fewer raw materials will be needed, which means less land, water and fertilisers are needed and CO2 emissions are reduced.”
Circular agriculture
Today, more and more agricultural residues are being put to good use, as businesses opt to invest more in circularity. The concept of circularity involves creating a world without waste. In a linear system, raw materials are lost during the production cycle, whereas in a circular system, as much as possible of these by-products are recycled. Biomass cannot usually be re-used indefinitely, because they always perish eventually. Circularity is also receiving increasing attention from the government. The Ministry of Agriculture, Nature and Food Quality has the task of encouraging circular agriculture with the support of agricultural councils both at home and abroad. There is still plenty of room for improving the circularity of the agrifood industry, according to Elbersen.
“Businesses often only consider what they think will be feasible, what will make them money, or what will solve an environmental problem. But circularity is more than that. The question is not whether a solution is circular or not, but whether it is the more circular solution.” Elbersen gives the example of composting. The nutrients are returned to the soil and organic matter is replenished. “But that solution makes me feel something is missing. Could we do it better and more efficiently by using that compost in another application first, and only then returning the nutrients and stable organic matter to the soil?” he wonders. “I often hear people say: We are 100% circular. I think that’s an odd statement, because some solutions are more circular than others.”
We make it easier for policymakers and businesses by giving them tools to work with
Assessment framework
Elbersen sees that the choice for circular solutions is often made with too narrow a view. Businesses only want to know whether these solutions are financially beneficial or solve a problem. “These are important questions, but it is actually much more complex. We have now created a comprehensive assessment framework to help them choose. On the one hand, we are making it more difficult for policymakers and businesses, because they have more options to consider. But on the other hand we are also making it easier, by providing them with tools,” says Elbersen.
Maintaining functionality
The new assessment framework takes various aspects of circularity into account, such as the functionality of the components, and whether this functionality is retained. For example, you can burn wood residues directly for energy, but you can also first make a table, or products from pressed wood, and then use the cellulose to make clothes. Finally, at the end of the chain, you can burn the fibre for energy production. In each step, the wood is broken down further, but still retains its functionality for the next application. “Down-cycling is unavoidable with bio-based materials, but if you preserve the functionality as much as possible after each stage, it increases the options for re-using the material instead of having to use new raw material,” says Elbersen.
Other aspects that are taken into account are process efficiency, options for reuse and reducing land use. The thinking behind this is that the longer a material remains in the cycle, the less land (water, nutrients, labour) will be needed. Burning wood without first using for other purposes costs more trees because it means other trees have to be grown to make the wooden products.
Components
For each biomass component (fibre, sugars, starch, protein, fats, oils and nutrients), a hierarchy has been drawn up which describes which applications should be used first and which can better be left until the end. End-of-life applications are not at the bottom because they are unimportant, but because they can be more efficiently deployed at this later stage. Elbersen suspects that many users of the assessment framework will not be used to looking at individual components. In the case of protein, an application in food or feed is often the most circular solution, but this need not be the case for fibres.
Organic residues increase soil quality by returning nutrients like phosphate and potassium to the soil and replenishing organic matter
Back to the soil
In many cases, the soil is the last destination of a material, because food, fodder and other applications take precedence. “That does not mean that maintaining soil quality is not important,” says Elbersen. “It is important to return organic matter and nutrients like phosphate, potassium and nitrogen to the soil. But you can still decide to do other things with crop residues first, as long as you do not lose those nutrients. Phosphate and potassium are non-renewable resources. So you want to put those back into the soil, where this is needed.”
But returning that biomass directly to the soil is less efficient, and can even be problematic, as is demonstrated by sugar beet harvesting. The leaves remain behind on the field after the harvest and are therefore of value to the soil, but on sandy soils the nutrients leach out before they can be used by the new plants in the spring. “Moreover, hundreds of kilograms of protein are not used as such, but as fertiliser instead. These proteins could also be refined and used for functional food products. The rest can be used to produce biogas for energy. In the spring you can then return the remaining digestate to the field,” Elbersen explains.
Implementation
This solution for sugar beet leaf is not easy to carry out. “Farmers are only allowed to apply a limited amount of nitrogen and phosphate fertiliser each year. The reintroduction of the previously removed N and P is often not permitted. That’s why they often choose to let the leaves lie in the field.” This makes it more difficult to implement more circular methods. In addition to regulations, the lack of the right infrastructure or technology can also be an obstacle. So, such aspects of implementation have also been included in the assessment framework. “This is where the government can step in,” says Elbersen.
The framework is a tool, but the user still needs to interpret the result
Any comparison of a new and an existing application of an agricultural residue requires careful consideration of the various factors. Some aspects may not be important in a particular case, while others may weigh more heavily. For example, loss of nitrogen to the environment is very relevant in the Netherlands. “The framework is a tool, but the user still needs to interpret the result,” says Elbersen. He and his colleagues are now working on the next step: a model that calculates the circularity of a process. That will require less interpretation by the user. Elbersen expects that it will then become easier to identify the most circular applications for agricultural residues.